武州工業株式会社 ‐ 「1個流し生産」などアイデア経営が光る武蔵国の雄
武州工業株式会社 ‐ 「1個流し生産」などアイデア経営が光る武蔵国の雄
◆取材:綿抜幹夫 /文:渡辺友樹
武州工業株式会社/代表取締役 林 英夫氏
国内生産で成長を続けるパイプ曲げ加工・板金加工メーカー
日本企業の海外進出が相次ぐ中、自社製の機械設備や独自の生産システムなど徹底的なコスト削減で競争力を付け、日本国内で成長を続けるのが「武州工業株式会社」。
自己資本比率は5割を超え、優良申告法人として表敬され続けている。コンサルを入れずに自分たちですべて考えるという同社の経営は、製造業・中小企業のヒントとなるアイデアに溢れている。
◎自動車部品に加え、医療機器へも参入
■メカトロニクス
1952年、同社設立と同じ年に生まれた同氏。日本大学生産工学部電気工学科を卒業後、現在でいうメカトロニクスを用いた初のカメラ「エレクトロ35」を生み出したカメラメーカー、株式会社ヤシカ(長野県諏訪市)に入社する。
武州工業株式会社に入社したのは1978年。創業者である先代社長は機械が専門、同氏は電気工学が専門だったため、これらを融合し、メカトロニクスの機械設備を作るようになる。「ミニ設備」に代表される特徴的な同社の機械はすべてメカトロニクス。のちに「勇気ある経営大賞」を受賞する同社が成し遂げた低コスト化には、こうした土壌があった。
■自動車部品のパイプ
「1直・8時間・20日」の労働環境を目指す「8・20体制」に留まらず、同社ではさらなる従業員満足度の向上を図っている
同社の本業は自動車部品用のパイプ曲げ加工。創業63年の歴史には山もあり谷もあったが、同氏は「当社は、世の中よりも落ち込み方が遅くて小さく、そこからの立ち上がりも世の中より早い」と語る。
たとえば、バブル崩壊のときもそうだ。2000年、カルロス・ゴーン氏が日産の社長に就任し、リストラクチャリングを行った。
簡単に言えば、儲からない仕事をカットし、儲かる仕事に専念するのがリストラクチャリング。部品メーカーにとって、その儲からない仕事がパイプ加工だった。
バブル期に、増え続ける生産台数に生産が追いつかなくなり、下請けへの発注のみならず自社生産も行うようになったが、バブル崩壊でそれが過剰設備となり手放したのだ。このとき、手放された5社7工場のパイプ部品を設備ごと・仕事ごと引き受けた同社は、バブル崩壊の翌年から4年間、売り上げが伸び続けたという。
■医療機器分野への参入
かつては同社の売り上げのほぼ100%を占めていた自動車部品は、現在約半分の54%。とはいえ、自動車部品は減ったわけではなく、微増を続けている。新たに医療機器へ参入し、大きく伸ばしたのだ。
自動車部品は、安価で数の出る大量生産だ。しかし、本来医療の分野は異なる。医療機器の利用者は医療関係者に限られ、その中でも診療科ごとに細分化されている。
自動車と比べてはるかに小さなマーケットで、ひとつの部品が月産300本程度にすぎない。同社が医療分野に参入したのは、内視鏡下外科手術の処置具に使うディスポーザブル(使い捨て)のパイプ製品を受注したから。
前述のような小さなマーケットを相手にしていた医療用パイプ製造業者は、月産数万本に及ぶというディスポーザブル部品の生産能力がなかったのだ。
しかし、同社は長年自動車部品を月産90万本ほど生産してきた。しかも、コスト削減で利益を出す熾烈な自動車業界が主戦場だ。生産量も、見積もりも、桁違いの能力を持っていた。こうして医療分野の仕事が増え、2011年から2014年までの間に売り上げ全体の40%を占めるまでに成長したのだ。
■自社製品「パイプグラム」
グッドデザイン賞2014、iFデザインアワード2015を受賞した「パイプグラム」。写真は、硬さのある黒いジョイントでしっかりとした立体をつくることができる「ベーシックセット・B」による20面体
2014年には、デザイナーの小関隆一氏とのコラボによる知育玩具「パイプグラム」を発売、B to Cにも乗り出した。
小さなパイプを組み立ててさまざまな形を作る、いわばパイプ版「ブロック遊び」ができる玩具だが、そのデザイン性や品質の高さ、また自由度の高さから、大人も遊べる知育玩具として注目を集めている。
パイプグラム誕生のきっかけは、モノづくり企業とデザイナーとをつなぐコンペティション「東京ビジネスデザインアワード」だった。2013年、同アワードにパイプ曲げ加工技術で応募した同社に、10人のデザイナーが知育玩具を提案。その中から、「このアイデアなら、小さい頃からモノづくりに親しんでもらえると思った」という小関氏のパイプグラムが採用されたという経緯だ。
自社製品を持つことでさらに安定した経営を図ると同時に、高齢化や後継者不足に悩む製造業の未来の担い手を育てる意義もある。日本発のモノづくり玩具、パイプグラムに期待がかかる。
◎「1個流し生産」
■1個流し生産
ほかにも、柔らかな白いジョイントで作品の変形が可能な「ベーシックセット・W」や、オリジナルカーブのパイプで真鯛・カエル・だるま(写真)などの形がつくれる「組み立てキット」がある
同社の最大の特徴は、1人の多能工が生産の全行程を担当する「1個流し生産」と名付けられた生産体制だ。1985年に導入し、人材育成やIT化を進めながら年々磨き上げてきた。
この1個流し生産を、スペックを絞った自社製の機械である「ミニ設備」で行うことでローコスト化に成功、少品種大量生産から多品種少量生産への変革に成功した。1個ずつしか作らず、在庫も抱えない。注文があった時点で生産する、中小企業ならではのフレキシブルなモノづくりだ。
日本の職人のモノづくりに着想を得たという「1個流し生産」。道具づくりも含めた工程の最初から最後まですべてを1人の職人が行うという特徴を取り入れ、同社の「1個流し生産」も、最低限の機能のみを持った「ミニ設備」を自社で作り、生産計画から品質保証まですべてを1人の多能工が担当する。
「1個流し生産は、フランチャイズのラーメン屋さんのイメージです。フランチャイジーの親方が私で、1人ひとりが店長です。
もちろん、社としてのベクトル合わせは行いますが、品質、コスト、納期、開発、マネージメントなど、任せている範疇が大きいわけです。
ラーメン屋さんで、ラーメンにゴキブリが入っていると困りますよね。自分のラーメンに入っていたら、作り直せと返します。でも、周りで食べている人は自分のラーメンには入っていないから平気です。なぜ自分のラーメンには入っていないことがわかるかというと、ラーメンは1杯ずつ作っているからです。
これが大量生産だった場合はカップラーメンと同じですから、1つに入っていたらすべてを疑わなくてはならない。1個ずつ作っていれば、どこに入っているかわかるんです」
■3Z保証
ベーシックタイプのパイプやジョイントにはレフィルも用意されている
「1個流し生産」は、1個ずつ作っているため検査の工程を設けていない。1個流し生産で作った製品が完成に至ったということは、すなわちすべての工程が正しかったことを意味するからだ。
問題のある製品が完成に至ることはなく、完成した時点で100%保証されているため、そのままトラックに積んで発送してしまう。これが1個流し生産でなければ、生産工程とは別に検査のプロセスを設け、何度も検査を行わなければならない。ここにも、同社のコスト削減のアイデアがある。
同社の1個流し生産では、検査がない代わりに、工程内で「3Z保証」という品質保証をしている。3Zとは、「作らず、流さず、受け取らず」の3つのZから成る。設備や金型といった工程能力の部分で保証するのが「作らず」だ。
そして機械や金型の不具合によって不良品が出た場合には「流さず」という工程内のチェックが入り、次の工程に流れない。そして前工程、購入部品などに不具合があった場合に受け取らないようにする仕組みが「受け取らず」だ。1個流し生産は、独立した検査プロセスを工程内に組み込んでしまうことで、コストをカットしているのだ。
◎完全国内志向で優良企業であり続ける
■良好な労働環境、優良申告法人
同社は「8・20体制」と名付け、「1直・8時間・20日」の労働環境を目指している。「1直」はすでに実現し、年間勤務日数が245日のため「20日」もほぼ実現している。8時から17時までを定時とする「8時間」勤務についても、水曜日はノー残業デーであるほか、多少の残業もクライアントの都合などやむを得ない範囲にとどめている。
また、税務内容も良好な同社は1968年から赤字決算がなく、5年に1度の優良申告法人の表敬を7度受けている。7度の表敬は、所属する立川法人会1万2千社中、わずか2社だ。
■勇気ある経営大賞
2012年、東京都商工会議所が主催する「勇気ある経営大賞」を受賞した同社。「1個流し生産」と医療分野への挑戦が評価されての受賞となった。4次審査に臨んだ同氏は、「国内で世界に通じるコストの自動車部品を製造すること、それが当社の勇気ある経営」と述べたという。
自動車業界には「LCC」という言葉がある。「Low Cost Country」、世界で最も安い国の価格をグローバルプライスとし、生産地がどこの国であっても、その値段で作るという考え方だ。
中小企業までもが海外生産に踏み切る状況だが、日本でその値段で作れるのであれば、海外に行く必要はない。国内でLCC価格の生産を行え、「8・20体制」で労働環境も良く、優良申告法人として社会貢献ができれば、海外に出る必要がない。
同社は見事にそれを実現し、なんと5割超の自己資本比率というバランスシートを達成している。さまざまなアイデア経営は、すべてこれを実現するためだ。
■アタックV活動
同社が5期ごとにテーマを決めて取り組む中期戦略が「アタックV活動」だ。1985年に始めた「アタックV活動」、過去には1個流し生産やミニ設備などを含む「限りなきコストダウン」のほか、3Z保証での「不良ゼロへの挑戦」、その後は「頼れる職人企業へ」「感動のサービスを提供する」などをテーマに定め、取り組んできた。
今期の5年間は「おもてなしの心で」だ。3Z保証で行ってきた工程内品質保証の更なる精度アップのため、「目指せAランク」を目標に設定。Cランクは目視確認、Bランクは治工具を用いて確認、Aランクは人の判断を伴わない自動全数検査だが、すべての設備でAランクを導入することを目標としている。
このほか、従業員へのおもてなしという意味で、「8・20体制」に留まらず従業員満足度の向上を図っている。昨年には、パートを0にし、全員を正社員登用した。手厚い給与体系のほか、育児や介護を行っている社員のために時短制度も導入するなど、働きやすい職場づくりに努めている。
◇
2013年には、医療機器分野の更なる拡大を見越して新たに工場を竣工。長年培ってきたノウハウと若手社員の柔軟な発想を生かし、これからも挑戦の手は緩めない。同社の経営は、日本の中小企業や製造業に大きなヒントとなるアイデアに溢れている。まだまだ、国内でできることがある。
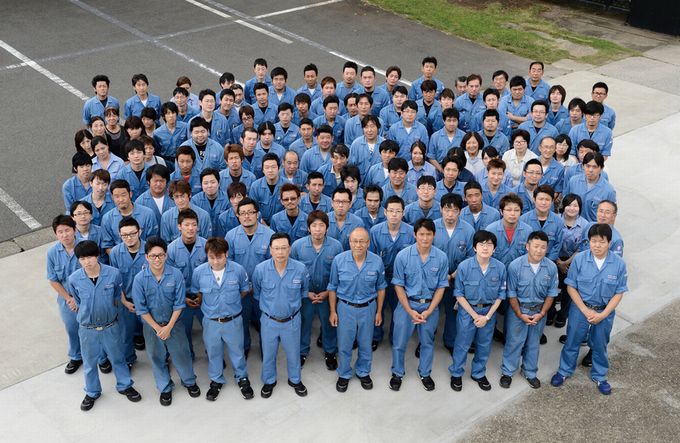
5期ごとに定めたテーマに沿った活動を進める「アタックV活動」。今期は「おもてなしの心で」を活動テーマとし、顧客と密接なコミュニケーションを図りながら工程内品質保証体制を確立していくことなどを目標として、社員一丸となり取り組む。写真:工場
◉プロフィール
林 英夫(はやし・ひでお)氏
1952年 東京都生まれ。
1974年 日本大学生産工学部電気工学科卒業。 株式会社ヤシカ入社。
1978年 武州工業株式会社入社。
1992年 代表取締役。現職。
◉武州工業株式会社
〈本 社〉
〒198-0025 東京都青梅市末広町1-2-3
TEL 0428-31-0167